Overall Equipment Effectiveness (OEE) is more than a metric; it's a comprehensive reflection of a manufacturing operation's utilisation against its full potential. It's the heartbeat of a plant's productivity, shedding light on the percentage of manufacturing time that contributes to actual, valuable output. In an era where every second and resource counts, understanding OEE is vital for any manufacturing entity aiming to optimise its operations, reduce wastage, and ensure that every component contributes positively to the end goal.
What is OEE?
Overall Equipment Effectiveness is a critical performance metric used to evaluate the efficiency and effectiveness of manufacturing processes. OEE highlights areas where the manufacturing process needs to be improved.
It encompasses three essential factors: availability, performance, and quality.
Availability: This is the measure of how often your equipment is ready and available for production versus the planned production time. It's affected by various factors, including equipment breakdowns, maintenance, and setup time.
Performance: This component assesses whether your equipment operates at the maximum possible speed, and how often it's interrupted by small stops or slow cycles.
Quality: Quality measures the production of good, sellable products versus the total output, including defective items. A high-quality score means you're producing a larger percentage of good, sellable products.
How do you calculate overall OEE?
The OEE score is calculated with a straightforward formula:
OEE = Availability x Performance x Quality.
Each metric is given a percentage score out of 100, and these are multiplied together to reach your OEE score
For example:
Availability = 90%
Performance = 85%
Quality = 95%
0.9 x 0.85 x 0.95 = 0.76 (x100) = 76% OEE score
Despite what you’d think, 85% is generally considered world class manufacturing. It is extremely hard to achieve a 100% score, as this would mean manufacturing only good parts, as fast as possible, with no stop time.
Machines will naturally experience wear and tear, often where it can’t be foreseen, so it's It’s very difficult to have all machines functioning at their optimal rate, 24/7, without any issues.
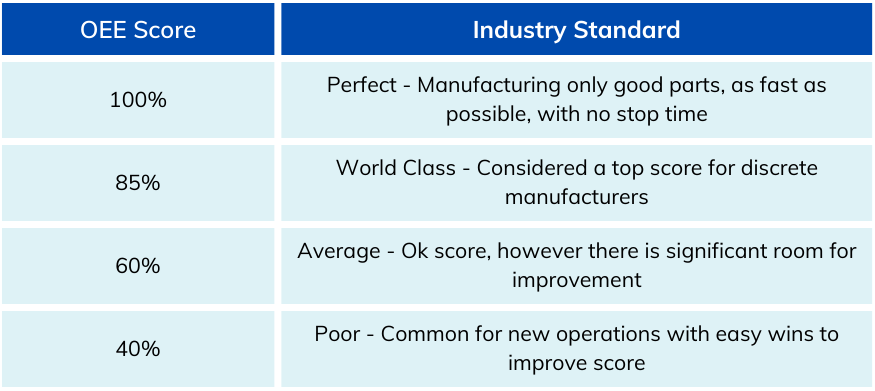
For a deeper look into how to calculate OEE, check out our comprehensive calculating OEE guide.
How is each factor of OEE calculated?
Each factor of OEE has its unique impact and measurement methods.
Availability is typically calculated by the following:
Availability = actual operating time / planned production time
The main factors that reduce availability are equipment failures, setup and adjustments, and unplanned maintenance.
Performance takes into account:
Performance = ideal cycle time (the fastest possible time to produce one item) / the actual cycle time
It's reduced by factors like minor stops, reduced speed, and idling times.
Quality is measured by:
Quality = good units / total units
Quality is affected by defects and any production that doesn't meet quality standards.
By focusing on these three metrics, the entire manufacturing process will be covered and you’ll be able to identify areas for improvement.
How can I Improve OEE?
To boost OEE, it's crucial to understand and tackle the losses that affect availability, performance, and quality. These often fall into six categories:
- Equipment failure
- Setup and adjustments
- Idling and minor stops
- Reduced speed
- Process defects
- Reduced yield
Identifying the most significant losses in your operation and implementing targeted strategies to mitigate them can lead to substantial improvements in OEE.
What tools can I use to improve OEE?
Adopting best practices and utilising tools can significantly aid in improving OEE. Implementing manufacturing analytics software can help to analyse cycle time, quickly identify causes of downtime, and provide key insights into areas of improvement. Busroot, developed by output.industries, offers manufacturers real-time monitoring and data collection capabilities. By integrating with various systems and sensors, Busroot gathers comprehensive and accurate data on equipment performance, forming the foundation for OEE calculations.
Busroot automates the calculation of OEE based on real-time data and provides intuitive dashboards and visualisations, enabling manufacturers to track OEE trends, identify improvement opportunities, and make data-driven decisions.
Busroot supports manufacturers by providing alerts and notifications when OEE metrics deviate from targets or set thresholds. These alerts prompt manufacturers to address issues promptly, fostering a culture of continuous improvement and efficiency gains. If you’d like to find out more about Busroot, check out our features page.
OEE powering manufacturing excellence
Overall, OEE is a powerful metric that supports manufacturers in improving efficiency and maximising profits from their operations. It provides key insights into how the factory is performing, and helps to identify areas of improvement. Implementing manufacturing analytics software like Busroot by Output.Industries automates this process and supports manufacturers in their continuous improvement efforts. If you'd like to find out more about how Busroot can maixmise your operations, get in touch now and book a call with one of our manufacturing experts!